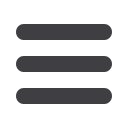
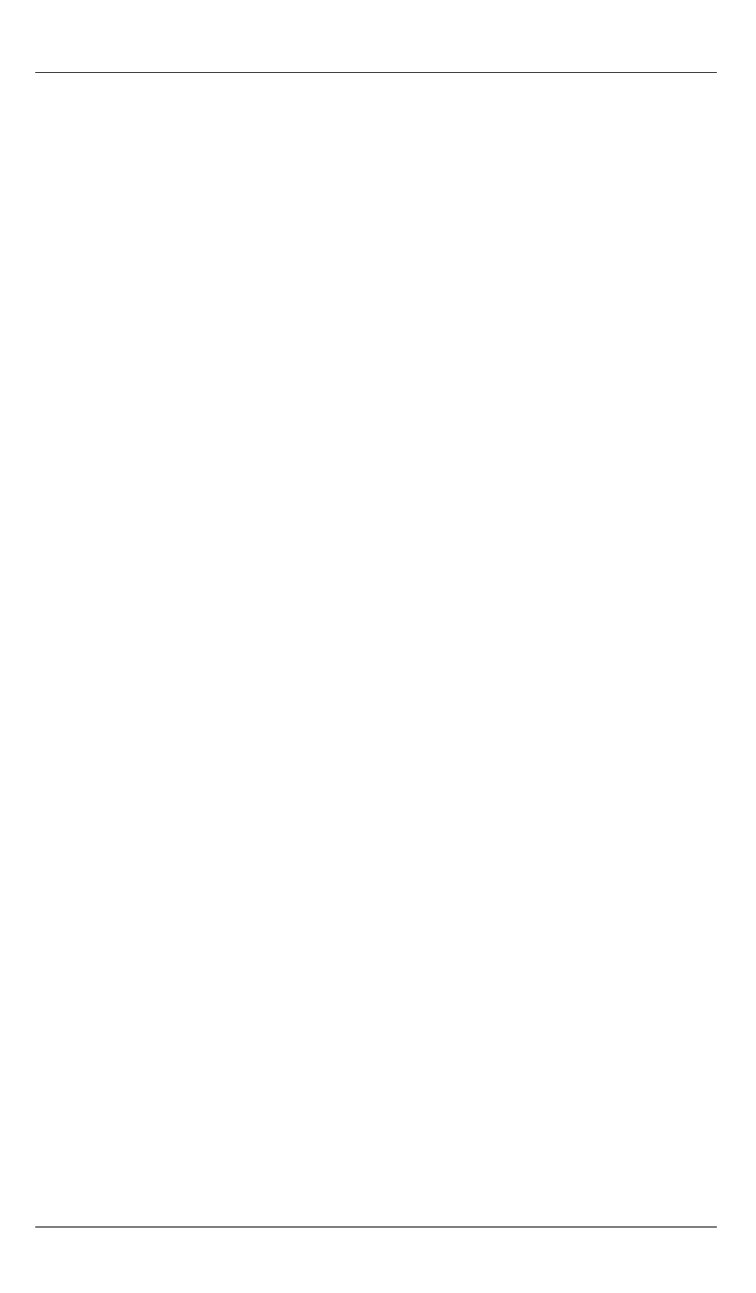
Перколяционная модель накопления микродефектов и коллапса…
Инженерный журнал: наука и инновации
# 11·2016 15
Percolation model of micro-defects accumulation and
forced elasticity area collapse before the crack fracture
front in polymer and composite materials
© A.A. Valishin
1
, I.V. Antonova
2
1
Bauman Moscow State Technical University, Moscow, 105005, Russia
2
Moscow Technological University, Moscow, 119454, Russia
The results of this study allow us to follow qualitatively and quantitatively all the induced
elasticity evolution stages before the crack front zone in polymeric materials. They are:
zone formation, micro-defects emergence, holes and their elastic field, interaction of the
holes, holes binding and fusion and the clusters formation, the holes’ emergence process,
kinetics at the initial and advanced stages. In this paper we consider the elastic zone evo-
lution final stage: the formation of infinite holes’ cluster and the elastic band collapse.
The study considers induced elasticity zone hierarchical structure, formulates elastic
band collapse percolation test, and obtains an oriented amorphous-crystalline fiber con-
centration failure criterion and the resulting elastic band percolation test collapse simi-
lar to known in the literature. The ratio of these criteria is a universal constant with ac-
curacy of 2.58. Close to collapse almost all the holes are in a bound state, and the elas-
tic band is riddled in all directions with cracks network – channels that connect the holes.
At the collapse time the share of "damaged" holes of the elastic band is not more than
30% of the entire area, and it is riddled with channels and connecting holes.
Keywords:
crack, induced elasticity zone, micro-defects-holes, percolation, an infinite
cluster, the elastic band collaps.
REFERENCES
[1]
Dimitrienko Yu.I., Sokolov A.P.
Inzhenerny zhurnal: nauka i innovatsii
—
Engineering Journal: Science and Innovation
, 2012, issue 11. DOI:
10.18698/2308-6033-2012-11-427
[2]
Dimitrienko Yu.I., Sokolov A.P.
Matematicheskoe modelirovanie —
Mathematical Modeling
, 2012, vol. 24, no. 5, pp. 3–20.
[3]
Dimitrienko Yu.I., Sokolov A.P.
Matematicheskoe modelirovanie —
Mathematical Modeling
, 2010, vol. 2, no. 1, pp. 116–130.
[4]
Dimitrienko Yu.I. Thermal stresses and heat mass-transfer in ablatingcomposite
materials.
International Journal of Heat Mass Transfer
, 1995, vol. 38, no. 1,
pp. 139–146.
[5]
Dimitrienko Yu.I. Thermal Stresses in Ablative Composite Thin-Walled
Structures under Intensive Heat Flows
. International Journal of Engineering
Science
, 1997, vol. 35, no. 1, pp. 15–31.
[6]
Valishin A.A., Stepanova T.S.
Inzhenerny zhurnal: nauka i innovatsii
—
Engineering Journal: Science and Innovation
, 2012, no. 2 (2). DOI:
10.18698/2308-6033-2012-2-52
[7]
Valishin A.A., Stepanova T.S.
Inzhenerny zhurnal: nauka i innovatsii
—
Engineering Journal: Science and Innovation
, 2013, no. 9 (21). DOI:
10.18698/2308-6033-2013-9-1119
[8]
Looyehl M.R.E., Samanta A., Jihan S., McConnachie. Modeling of reinforced
polymer composites subject to thermo-mechanical loading.
Int. Journal for
Numerical Methods in Engineering
, 2005, vol. 63, no. 6, pp. 898–925.